IMPブロックの性能評価
形状・外観確認
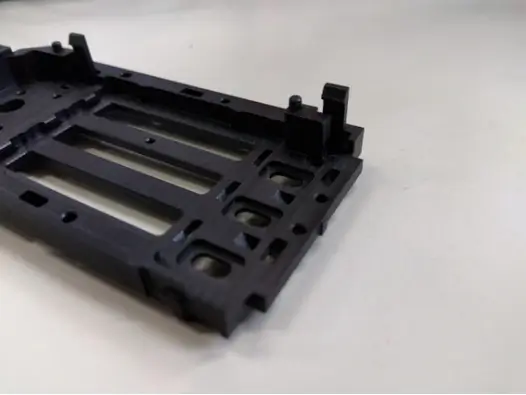
試作検証の役割の主な目的に形状や外観の確認があります。
- 形状の確認には様々な要件があります。勘合の確認や部品を組み合わせた際の動作確認などです。樹脂は粘弾性の特徴を持っており、金属とは明らかに異なる特性です。これらを上手く調整することで良好な製品作りが行えます。
- 外観の確認は見た目、触れた感覚、総合的な大きさや重さなどです。ユニバーサルデザインの観点からも確認を怠りたくないところです。
光学検証
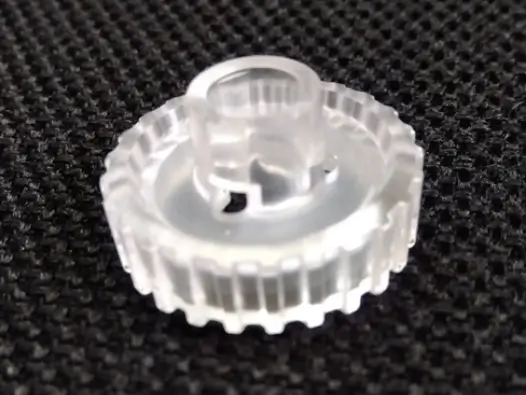
透明樹脂や光拡散樹脂などは光学部品として使用されるケースがあります。高い寸法精度を求められる場合は樹脂ブロックからの切削加工が有効です。切削加工により部品として使用する場合もありますが、光学特性の検証用としてIMPブロックは広く使われています。
近年、光拡散グレードが充実しています。光源を直接透過しない材料であり、その拡散度も様々です。実際に同材料により作られた部品により確認する必要があります。
耐熱性確認
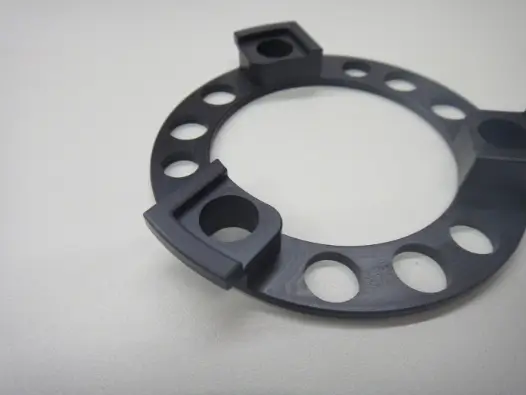
樹脂材料の耐熱性は金属とは明らかに異なります。粘弾性体である樹脂は環境温度でその性質が変化してまいります。部品に加わる応力や部品の形状などに依存する部分であり、正しい材料で検証する必要があります。
近年では様々な分野で金属製品の樹脂化が進み、材料メーカーも様々な新材料や添加剤による改質を手掛けています。金属部品の樹脂化に挑戦する環境が整いつつあります。
高強度樹脂
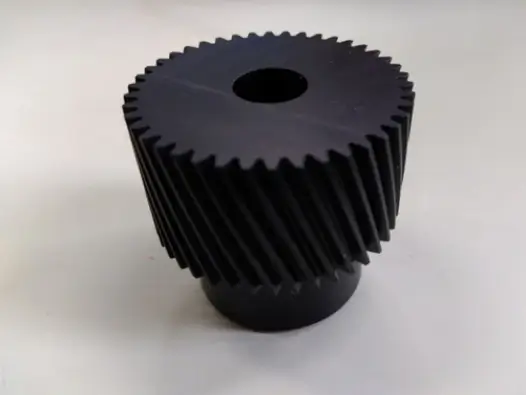
強度検証は製品作りには欠くことのできない要件です。製品使用時の破損などは事前の確認が必要です。IMPブロックにより高密度で製作した素材を切削加工することは射出成形で製造した部品と比べ若干の強度低下が観られます。そのことは切削加工で製造した部品において耐久性が満足した場合、射出成形では問題ないことを示します。
樹脂材料は力が加わると金属と比べて大きく変形することが予想されます。その変形が組み立て品の機能低下を招くなどの検証を行います。
但し、射出成形で製造した部品において、ボイドや誤ったゲート位置などは事前の対策が必要です。
軟質樹脂
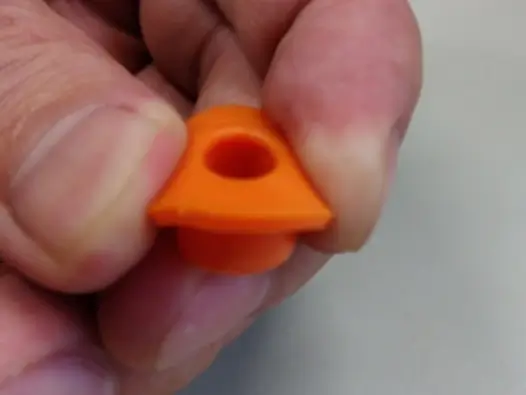
IMPブロックは軟質材料をブロック化できる唯一の方法です。
軟質材料はゴムとは異なり、復元力が弱いことから使い方には注意が必要です。
特に軟質樹脂では肉厚の違いや硬度の差により部品そのものの強度に大きな差が現れますので、量産前の検証が欠かせません。
尚、軟質材は切削加工に専門のノウハウが必要です。簡単に取り組めるものではございませんのでご注意願います。
摺動性樹脂
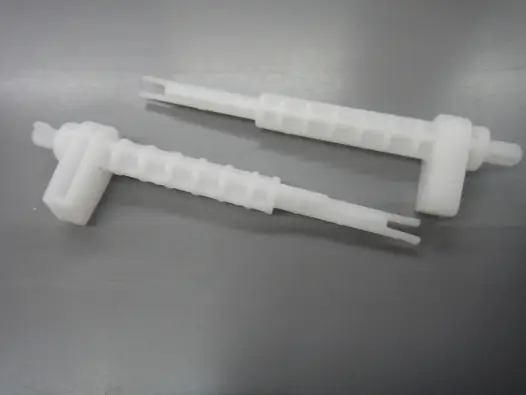
樹脂の持つ特徴の一つに摺動性があります。樹脂自身に摺動性を持たせ、コーティングなどの2次加工が不要であることが強みになります。近年ではフッ素を添加した材料や含油樹脂なども開発されており用途により使い分ける必要があります。
検証の重要項目が摺動性樹脂部品とそれに接する他部品の材質との相性になります。摩擦係数と押し当て力の検証はとても大切になります。
また樹脂の欠点は強い押し当て力の場合、樹脂表面が削られ粉となり摩擦係数が上がることで摺動時に鳴きや摩滅が生ずるなどの現象です。これらの検証はとても大切です。
耐薬品性確認
樹脂部品の使用範囲が広がりをみせております。様々な環境下での耐性の確認が必要です。特に耐薬品性は樹脂部品を使用する上では欠くことのできない検証要件です。例えば自動車部品において車両下回り部品では塩化カルシウムに対する耐性を確認することがマストとなります。
IMPブロックは切削加工を施すことで、強度検証などが行えますが、切削面は射出成型品のそれとは異なる微細な凹凸があり、その結果、薬品の浸食が促進することで耐薬品性の評価には向いていません。比較検証程度であるとお考え下さい。

お問い合わせ
樹脂製品、プラスチック製品の設計・成形の
お困りごとをご相談ください。